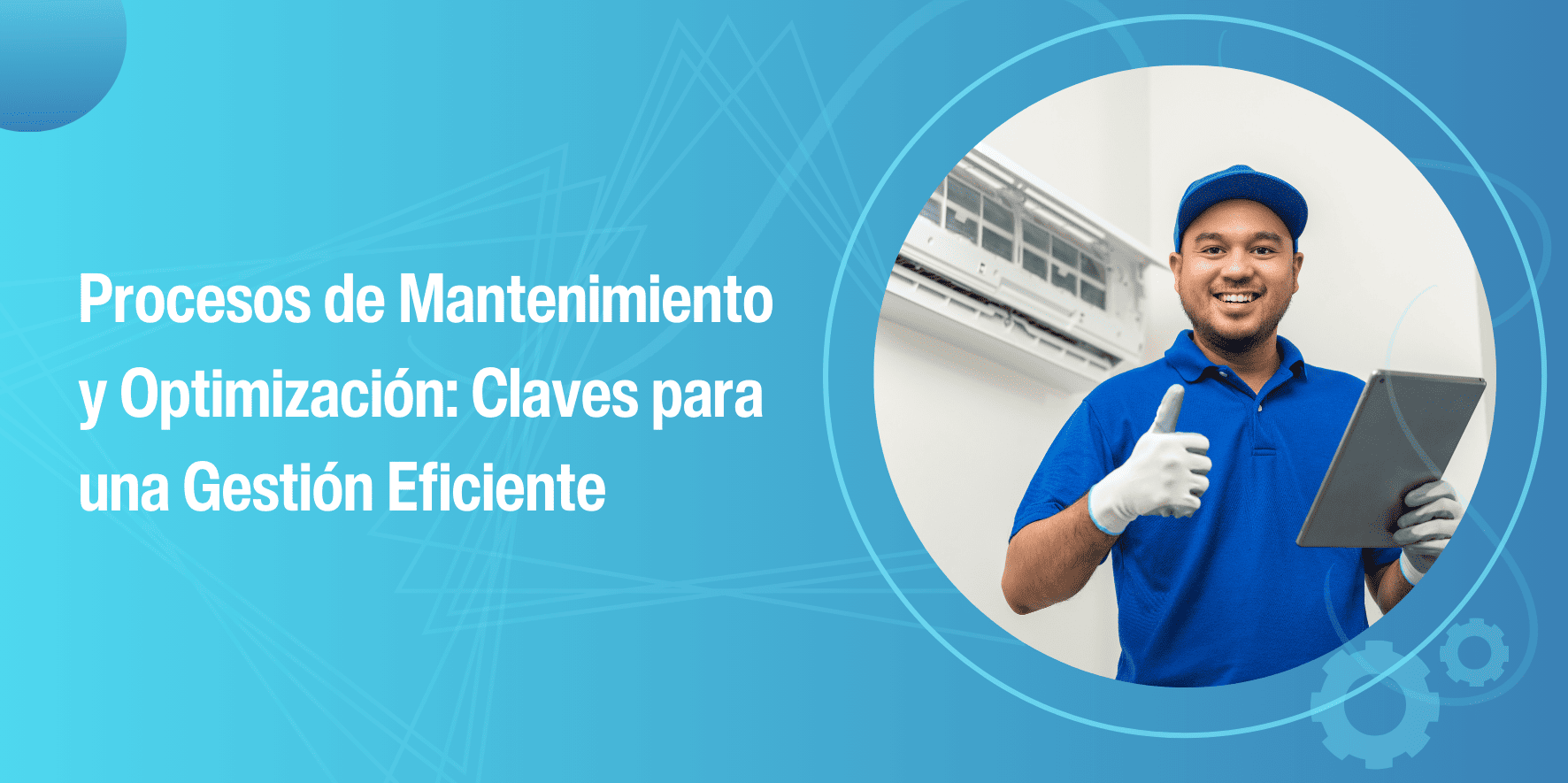
El mantenimiento industrial es un pilar fundamental para garantizar la continuidad operativa, la seguridad y la eficiencia en cualquier planta de producción. Sin una estrategia adecuada de mantenimiento, los activos pueden sufrir fallas inesperadas, lo que impacta la productividad y aumenta los costos operativos. Además, la optimización de estos procesos es clave para mejorar la rentabilidad y prolongar la vida útil de los equipos.
En este artículo, exploraremos los diferentes procesos de mantenimiento y las estrategias de optimización que pueden aplicarse para mejorar la gestión de activos industriales.
1. Tipos de Procesos de Mantenimiento
Los procesos de mantenimiento pueden clasificarse en diferentes categorías según su enfoque y objetivo. A continuación, describimos los principales tipos:
1.1. Mantenimiento Correctivo
Es el tipo de mantenimiento más básico y consiste en reparar los equipos después de que han fallado. Aunque es un enfoque reactivo, sigue siendo necesario en algunas situaciones donde la falla no afecta significativamente la producción o cuando el costo de reparación es menor que el de implementar una estrategia preventiva.
🔹 Ventajas:
- No requiere planificación previa.
- Se aplica solo cuando es necesario, reduciendo costos iniciales.
🔹 Desventajas:
- Puede generar tiempos de inactividad prolongados.
- Aumenta el riesgo de fallas imprevistas y costos elevados.
1.2. Mantenimiento Preventivo
Este enfoque busca reducir la probabilidad de fallas mediante inspecciones y actividades programadas, como lubricación, ajustes y limpieza. Se basa en un cronograma establecido y en recomendaciones del fabricante o datos históricos.
🔹 Ventajas:
- Reduce el número de fallas inesperadas.
- Mejora la confiabilidad de los equipos.
🔹 Desventajas:
- Puede generar costos innecesarios si las intervenciones se hacen antes de tiempo.
- Requiere planificación y seguimiento continuo.
1.3. Mantenimiento Predictivo
Se basa en el monitoreo constante de parámetros clave (vibraciones, temperatura, consumo de energía, entre otros) para anticipar fallas antes de que ocurran. Este tipo de mantenimiento utiliza sensores y tecnologías como el análisis de datos y el Internet de las Cosas (IoT).
🔹 Ventajas:
- Permite programar intervenciones justo antes de que ocurra una falla.
- Reduce costos al minimizar reparaciones innecesarias.
🔹 Desventajas:
- Requiere inversión en sensores y software de análisis.
- Puede ser complejo de implementar sin un equipo capacitado.
1.4. Mantenimiento Centrado en la Confiabilidad (RCM)
El RCM analiza el impacto de cada posible falla en la operación y determina la estrategia de mantenimiento más adecuada para minimizar los riesgos y costos. Este enfoque prioriza los activos más críticos y asigna recursos de manera eficiente.
🔹 Ventajas:
- Maximiza la confiabilidad y disponibilidad de los activos.
- Optimiza el uso de recursos y reduce costos operativos.
🔹 Desventajas:
- Su implementación puede ser compleja y requerir análisis detallados.
- Necesita una base de datos sólida y actualizada.
1.5. Mantenimiento Autónomo
Es una estrategia en la que los operadores de los equipos asumen tareas básicas de mantenimiento, como inspección, limpieza y lubricación. Esto permite una detección temprana de anomalías y mejora la cultura de mantenimiento en la empresa.
🔹 Ventajas:
- Reduce la carga de trabajo del equipo de mantenimiento.
- Fomenta la responsabilidad y el conocimiento técnico en los operadores.
🔹 Desventajas:
- Requiere capacitación constante.
- Puede haber resistencia por parte del personal operativo.
2. Estrategias de Optimización del Mantenimiento
Implementar estrategias de optimización es esencial para reducir costos, aumentar la eficiencia y mejorar la disponibilidad de los activos. Algunas de las mejores prácticas incluyen:
2.1. Digitalización y Software de Mantenimiento (CMMS)
El uso de un Software de Gestión del Mantenimiento Computarizado (CMMS) permite automatizar procesos, programar tareas, gestionar repuestos y registrar el historial de mantenimiento de cada equipo.
📌 Beneficios del CMMS:
- Mayor control sobre las órdenes de trabajo.
- Reducción de costos por mantenimiento correctivo.
- Análisis de datos para mejorar la planificación.
2.2. Implementación de KPI’s en Mantenimiento
Los Indicadores Clave de Desempeño (KPI’s) permiten medir la eficiencia del mantenimiento y detectar oportunidades de mejora. Algunos KPI’s relevantes incluyen:
- MTTR (Tiempo Medio de Reparación): mide el tiempo promedio que toma reparar un equipo después de una falla.
- MTBF (Tiempo Medio Entre Fallas): indica la confiabilidad de los activos.
- Disponibilidad de Equipos: porcentaje de tiempo en que un activo está operando sin fallas.
2.3. Gestión de Repuestos y Almacén
Un inventario eficiente de repuestos evita retrasos en las reparaciones y reduce costos de almacenamiento innecesarios. Para optimizar la gestión de repuestos:
✅ Identifica las piezas críticas y mantenlas en stock.
✅ Implementa un sistema de gestión de inventarios.
✅ Utiliza códigos QR o RFID para un mejor control.
2.4. Uso de Inteligencia Artificial y Big Data
Las tecnologías de IA y Big Data permiten predecir fallas, optimizar el mantenimiento y mejorar la toma de decisiones. Algunas aplicaciones incluyen:
🤖 Mantenimiento Predictivo basado en IA: análisis de patrones en datos históricos.
📊 Optimización de Programas de Mantenimiento: simulación de escenarios para maximizar la eficiencia.
📡 Monitoreo Remoto: sensores IoT para seguimiento en tiempo real.
2.5. Capacitación y Cultura de Mantenimiento
El factor humano sigue siendo clave en cualquier estrategia de mantenimiento. Capacitar al personal y fomentar una cultura de mantenimiento preventivo y autónomo puede hacer una gran diferencia en la eficiencia operativa.
💡 Recomendaciones:
- Realiza entrenamientos periódicos sobre mejores prácticas.
- Fomenta la detección temprana de anomalías.
- Incentiva la participación del personal en la mejora continua.
Conclusión
El mantenimiento industrial es un proceso dinámico que requiere estrategias bien definidas para garantizar la continuidad operativa y la eficiencia en los costos. Desde el mantenimiento correctivo hasta el predictivo y el RCM, cada estrategia tiene su propósito y aplicación según las necesidades de la empresa.
La optimización del mantenimiento mediante herramientas digitales, análisis de datos, gestión de repuestos y capacitación del personal puede marcar una gran diferencia en la competitividad de una empresa. Implementar un CMMS como EasyMaint permite llevar la gestión de mantenimiento a otro nivel, reduciendo costos y mejorando la confiabilidad de los activos.
🔧 ¿Tu empresa está optimizando correctamente sus procesos de mantenimiento? Un software especializado puede ayudarte a mejorar la eficiencia y evitar fallas inesperadas. ¡Empieza a optimizar hoy! 🚀