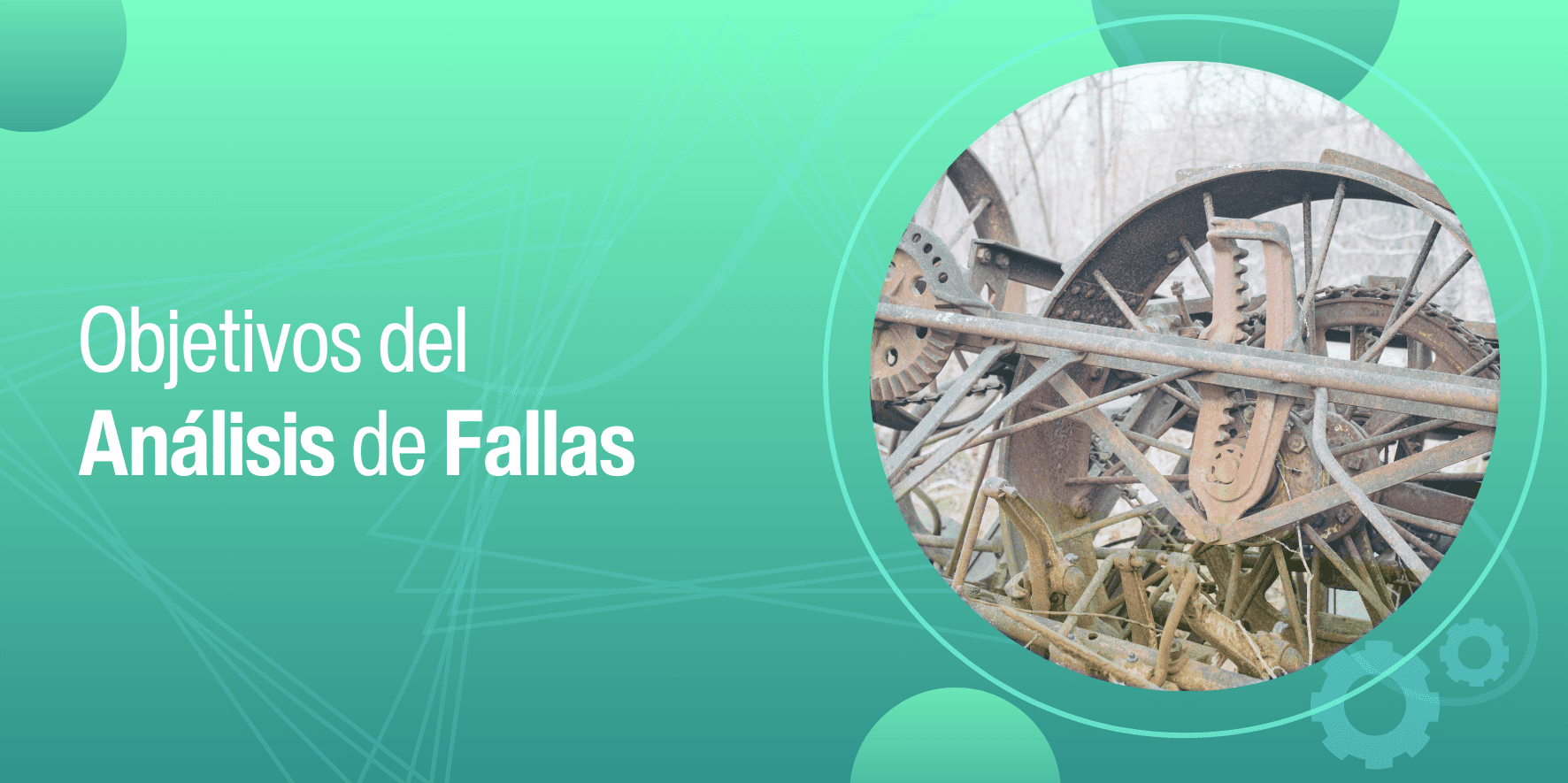
El análisis de fallas es un proceso crucial en la ingeniería y el mantenimiento industrial que tiene como objetivo identificar las causas fundamentales de los fallos en sistemas y componentes. Este proceso no solo se centra en detectar la falla, sino también en comprender su origen y prevenir su recurrencia. A continuación, se detallan los principales objetivos del análisis de fallas y su importancia en la mejora continua de sistemas y procesos industriales.
Objetivos del Análisis de Fallas
El análisis de fallas es un proceso crucial en la ingeniería y el mantenimiento industrial que tiene como objetivo identificar las causas fundamentales de los fallos en sistemas y componentes. Este proceso no solo se centra en detectar la falla, sino también en comprender su origen y prevenir su recurrencia. A continuación, se detallan los principales objetivos del análisis de fallas y su importancia en la mejora continua de sistemas y procesos industriales.
1. Identificación de Causas Raíz
Descripción
Uno de los objetivos primordiales del análisis de fallas es identificar las causas raíz que llevaron a un fallo. Este paso es fundamental para entender no solo lo que falló, sino por qué falló.
Importancia
- Prevención de Recurrencia: Al identificar y abordar la causa raíz, se pueden implementar medidas correctivas y preventivas que eviten que la falla se repita.
- Mejora de la Confiabilidad: Conocer la causa raíz permite mejorar el diseño y la operación de los sistemas, aumentando su confiabilidad y durabilidad.
2. Reducción del Tiempo de Inactividad
Descripción
Minimizar el tiempo de inactividad de los equipos es esencial para mantener la productividad y eficiencia en cualquier operación industrial.
Importancia
- Aumento de la Productividad: Reducir el tiempo de inactividad significa que los equipos están disponibles para producción durante más tiempo.
- Costos Reducidos: Menos tiempo de inactividad se traduce en menores costos operativos y de mantenimiento.
3. Optimización del Mantenimiento
Descripción
El análisis de fallas ayuda a mejorar las estrategias de mantenimiento, ajustándolas para ser más efectivas y eficientes.
Importancia
- Mantenimiento Preventivo: Permite planificar y ejecutar mantenimientos preventivos basados en datos y análisis, en lugar de esperar a que ocurra una falla.
- Recursos Eficientes: Optimiza el uso de recursos, asegurando que el mantenimiento se realice de manera proactiva y dirigida.
4. Mejora de la Seguridad
Descripción
La seguridad es una prioridad en cualquier entorno industrial. El análisis de fallas contribuye a identificar y mitigar riesgos antes de que se conviertan en incidentes.
Importancia
- Prevención de Accidentes: Identificar fallos potenciales y sus causas raíz ayuda a implementar medidas de seguridad que prevengan accidentes y lesiones.
- Entorno de Trabajo Seguro: Promueve un entorno de trabajo más seguro, reduciendo el riesgo de fallos catastróficos.
5. Optimización de Costos
Descripción
El análisis de fallas permite una mejor gestión de los costos asociados con el mantenimiento y la operación de equipos.
Importancia
- Costos de Mantenimiento: Identificar fallas y sus causas raíz puede reducir los costos de mantenimiento al prevenir fallas recurrentes.
- Costos de Producción: Minimizar el tiempo de inactividad y mejorar la eficiencia operativa reduce los costos de producción y aumenta la rentabilidad.
6. Mejora de la Calidad del Producto
Descripción
Las fallas en equipos y procesos pueden afectar la calidad del producto final. El análisis de fallas ayuda a mantener y mejorar la calidad.
Importancia
- Consistencia del Producto: Identificar y corregir fallas asegura que los productos se fabriquen de acuerdo con las especificaciones y estándares de calidad.
- Satisfacción del Cliente: Mejora la satisfacción del cliente al reducir defectos y mejorar la confiabilidad del producto.
7. Fomento de la Cultura de Mejora Continua
Descripción
El análisis de fallas es una herramienta clave en la filosofía de mejora continua, como el Kaizen en la manufactura.
Importancia
- Innovación y Mejora: Fomenta una cultura de innovación y mejora constante al identificar áreas de oportunidad y aplicar soluciones efectivas.
- Competitividad: Mejora la competitividad de la organización al mantener procesos eficientes y productos de alta calidad.
Métodos Comunes de Análisis de Fallas
Análisis de Causa Raíz (RCA)
El RCA es un método sistemático utilizado para identificar las causas fundamentales de una falla. Incluye técnicas como el diagrama de Ishikawa (causa y efecto), el método de los "5 por qués" y el análisis de fallos y efectos (FMEA).
Análisis de Modo y Efecto de Falla (FMEA)
El FMEA es una técnica proactiva que evalúa los modos de falla potenciales dentro de un sistema y sus efectos, permitiendo priorizar las acciones correctivas.
Análisis de Árbol de Fallos (FTA)
El FTA es un método deductivo que utiliza un diagrama en forma de árbol para representar las distintas combinaciones de fallos que podrían causar un evento no deseado.
Análisis de Datos
El análisis de datos históricos de fallos, mantenimientos y operaciones permite identificar patrones y tendencias, ayudando a predecir y prevenir fallos futuros.
El análisis de fallas es una herramienta indispensable para cualquier industria que desee mantener altos niveles de eficiencia, seguridad y calidad. Al identificar las causas raíz de los fallos, reducir el tiempo de inactividad, optimizar el mantenimiento, mejorar la seguridad y la calidad del producto, y fomentar una cultura de mejora continua, las organizaciones pueden lograr una ventaja competitiva significativa. Implementar estrategias efectivas de análisis de fallas no solo protege los activos y recursos de la empresa, sino que también contribuye al éxito sostenible y a largo plazo.