En el ámbito del mantenimiento industrial, adoptar un enfoque basado en la condición del equipo se ha convertido en una estrategia esencial para maximizar la eficiencia operativa y prolongar la vida útil de los activos. Mediante el uso de tecnologías avanzadas y análisis de datos, los equipos de mantenimiento pueden identificar problemas potenciales antes de que se conviertan en fallas costosas. Este artículo explora en detalle los ocho tipos de mantenimiento basado en la condición del equipo, que incluyen el análisis de aceite, el análisis de vibración, el análisis de circuitos motores, la termografía, la radiografía, la interferometría láser, el monitoreo eléctrico y la medición electromagnética. Estas técnicas, cuando se combinan con un software de mantenimiento confiable, pueden optimizar la gestión de activos y minimizar el tiempo de inactividad no planificado.
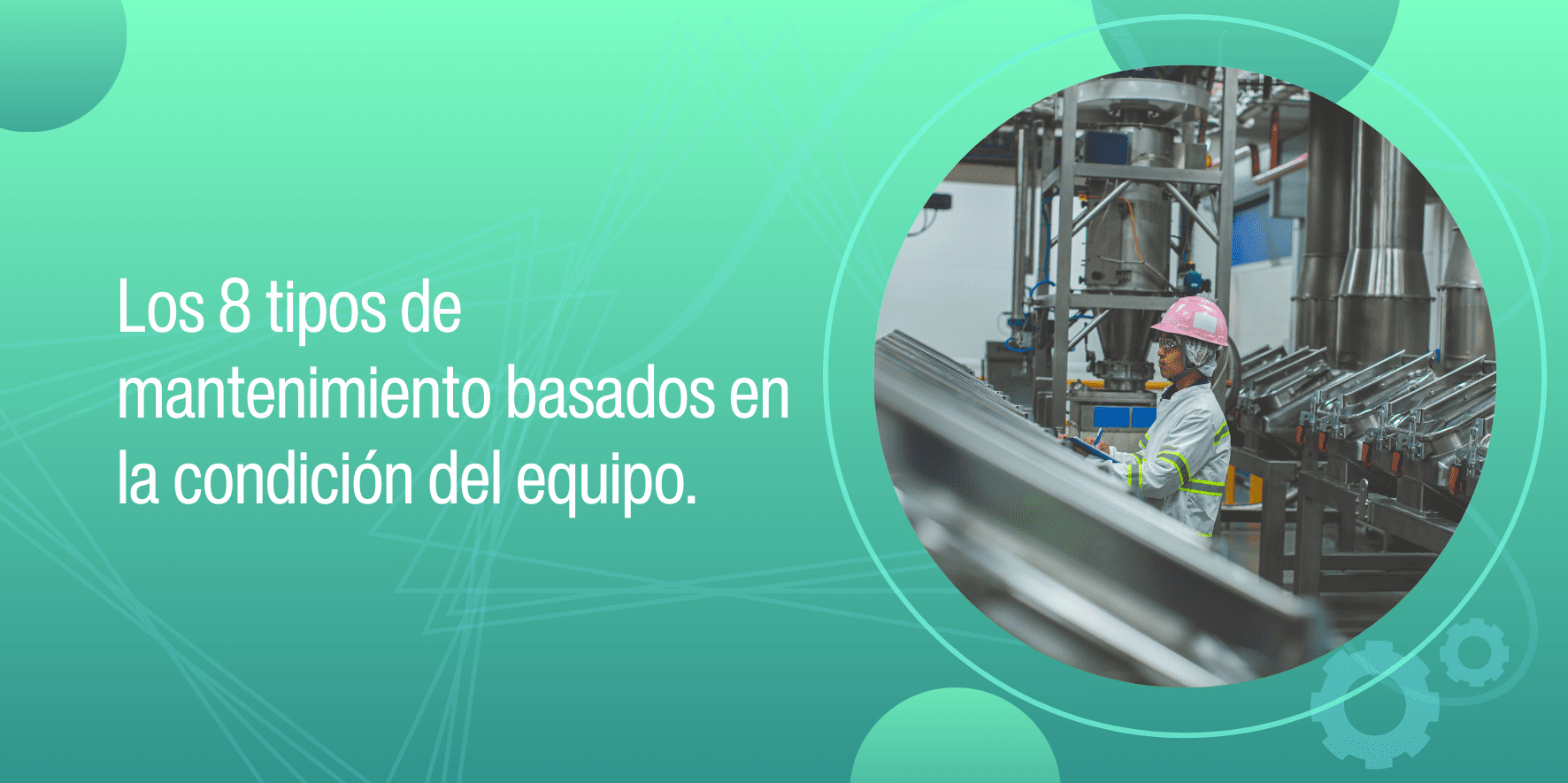
Los 8 tipos de mantenimiento basados en la condición del equipo. Una guía completa para optimizar tu gestión de activos
En el ámbito del mantenimiento industrial, adoptar un enfoque basado en la condición del equipo se ha convertido en una estrategia esencial para maximizar la eficiencia operativa y prolongar la vida útil de los activos. Mediante el uso de tecnologías avanzadas y análisis de datos, los equipos de mantenimiento pueden identificar problemas potenciales antes de que se conviertan en fallas costosas. Este artículo explora en detalle los ocho tipos de mantenimiento basado en la condición del equipo, que incluyen el análisis de aceite, el análisis de vibración, el análisis de circuitos motores, la termografía, la radiografía, la interferometría láser, el monitoreo eléctrico y la medición electromagnética. Estas técnicas, cuando se combinan con un software de mantenimiento confiable, pueden optimizar la gestión de activos y minimizar el tiempo de inactividad no planificado.
1. Análisis de Aceite
El análisis de aceite es fundamental para evaluar la condición de los lubricantes y los componentes del equipo. Al monitorear regularmente las propiedades físicas y químicas del aceite, como la viscosidad, la contaminación y el desgaste de los aditivos, se pueden detectar signos tempranos de desgaste o contaminación que podrían afectar el rendimiento de la maquinaria. Esta técnica permite tomar medidas preventivas antes de que ocurran daños graves.
2. Análisis de Vibración
El análisis de vibración se utiliza para medir las vibraciones mecánicas de los equipos rotativos. Cambios en los patrones de vibración pueden indicar desequilibrios, desalineaciones, holguras o desgaste en los rodamientos. Monitorear y analizar estas vibraciones permite identificar problemas potenciales y programar actividades de mantenimiento predictivo de manera oportuna, evitando fallos inesperados.
3. Análisis de Circuitos Motores
El análisis de circuitos motores se enfoca en monitorear y evaluar los sistemas eléctricos de los equipos. Este método detecta problemas como sobrecargas, desequilibrios de fases, fugas de corriente o altas resistencias en los contactos. Identificar y corregir estos problemas eléctricos puede prevenir el deterioro del equipo y reducir los riesgos de incendios o fallos catastróficos.
4. Termografía
La termografía utiliza cámaras infrarrojas para medir y visualizar diferencias de temperatura en los equipos. Esta técnica es eficaz para detectar puntos calientes, áreas de fricción excesiva o conexiones defectuosas en sistemas eléctricos. Identificar estas anomalías térmicas permite a los técnicos tomar medidas correctivas antes de que ocurran fallas costosas o incendios.
5. Radiografía
La radiografía en el mantenimiento industrial permite inspeccionar componentes internos sin necesidad de desmontar el equipo. Es especialmente útil para detectar grietas, corrosión o fallas en soldaduras en estructuras metálicas. Al proporcionar una visión interna precisa, la radiografía ayuda a prevenir fallos estructurales y garantiza la integridad de los equipos.
6. Interferometría Láser
La interferometría láser se utiliza para medir la precisión de los equipos y las instalaciones. Esta técnica puede identificar problemas en componentes mecánicos con alta precisión, ayudando a prevenir posibles fallas en el equipo. Es esencial para asegurar que los componentes mecánicos mantengan su alineación y funcionamiento óptimos.
7. Monitoreo Eléctrico
El monitoreo eléctrico mide la energía y la corriente eléctrica en los equipos y las instalaciones. Este tipo de mantenimiento ayuda a identificar posibles problemas en los circuitos eléctricos, como fluctuaciones de voltaje o corrientes anómalas, permitiendo una respuesta rápida para prevenir fallos en el equipo.
8. Medición Electromagnética
La medición electromagnética se utiliza para evaluar los campos magnéticos y eléctricos en los equipos e instalaciones. Al medir estos campos, es posible identificar problemas en los componentes eléctricos, como interferencias o fallos de aislamiento, previniendo posibles fallos y mejorando la seguridad operativa.
Cada uno de estos ocho tipos de mantenimiento basado en la condición del equipo desempeña un papel crucial en la gestión efectiva del mantenimiento. El uso de tecnologías como el análisis de aceite, análisis de vibración, análisis de circuitos motores, termografía, radiografía, interferometría láser, monitoreo eléctrico y medición electromagnética permite a los equipos de mantenimiento detectar problemas potenciales antes de que se conviertan en fallas graves y costosas.
Además, estos métodos ayudan a optimizar los programas de mantenimiento. Realizar un seguimiento regular de la salud y el rendimiento de los equipos permite establecer intervalos de mantenimiento más precisos, evitando tareas innecesarias o prematuras.
El uso de software especializado como EasyMaint refuerza estos tipos de mantenimiento, facilitando la recopilación, el análisis y el almacenamiento de datos, así como la programación de actividades de mantenimiento. Esto no solo mejora la eficiencia del proceso, sino que también permite una toma de decisiones más informada y basada en datos.
La combinación de estos ocho tipos de mantenimiento y el uso de un software adecuado puede marcar una gran diferencia en la confiabilidad, la vida útil y el rendimiento de los equipos. Al implementar estas prácticas de mantenimiento y tecnologías avanzadas, las empresas pueden reducir los tiempos de inactividad, aumentar la productividad y optimizar sus recursos, proporcionando un valor significativo a sus operaciones.