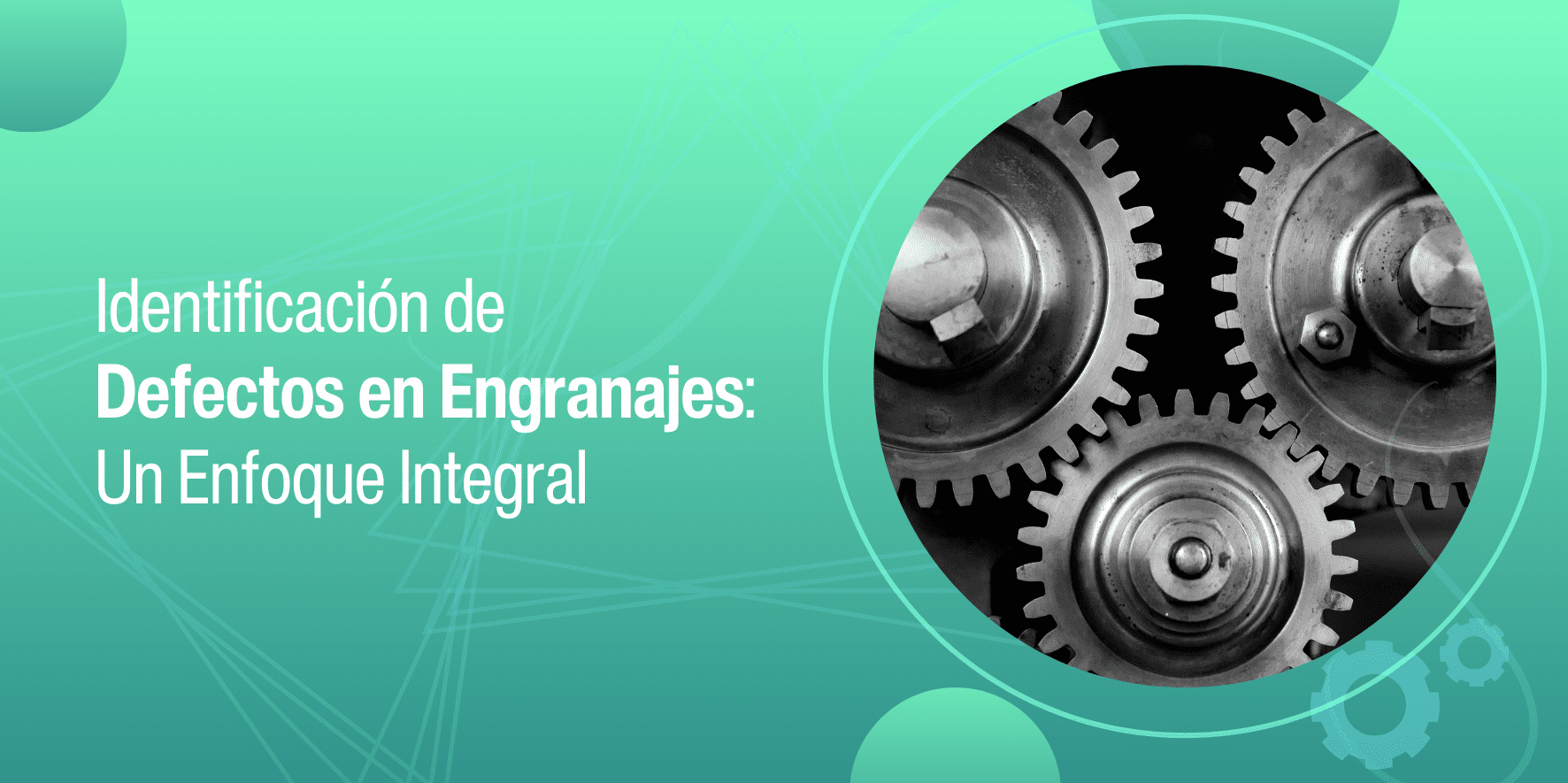
La identificación de defectos en engranajes es crucial para garantizar la eficiencia y durabilidad de los sistemas mecánicos. Los engranajes son componentes esenciales en una amplia variedad de maquinaria industrial, y cualquier defecto en ellos puede llevar a fallos catastróficos, tiempos de inactividad no planificados y costos de reparación significativos. Este artículo explorará las principales causas de defectos en engranajes, las técnicas de identificación y las mejores prácticas para la prevención y corrección de estos problemas.
Identificación de Defectos en Engranajes: Un Enfoque Integral
La identificación de defectos en engranajes es crucial para garantizar la eficiencia y durabilidad de los sistemas mecánicos. Los engranajes son componentes esenciales en una amplia variedad de maquinaria industrial, y cualquier defecto en ellos puede llevar a fallos catastróficos, tiempos de inactividad no planificados y costos de reparación significativos. Este artículo explorará las principales causas de defectos en engranajes, las técnicas de identificación y las mejores prácticas para la prevención y corrección de estos problemas.
Causas Comunes de Defectos en Engranajes
- Desgaste
- Desgaste Adhesivo: Ocurre cuando hay contacto directo entre superficies de engranajes sin lubricación adecuada, causando que las superficies se adhieran y luego se desgasten.
- Desgaste Abrasivo: Se produce cuando partículas duras de contaminantes o materiales abrasivos están presentes en el lubricante, causando el desgaste de las superficies de los dientes del engranaje.
- Fatiga de Superficie: Este tipo de desgaste ocurre cuando la superficie del engranaje se somete a cargas repetitivas, causando pequeñas grietas que eventualmente se convierten en picaduras o desconchados.
- Desalineación
- La desalineación de los ejes puede causar una distribución desigual de la carga en los dientes del engranaje, llevando a un desgaste prematuro y fallos en el engranaje.
- Sobrecarga
- Los engranajes sometidos a cargas mayores de las previstas pueden experimentar deformaciones plásticas y fallos prematuros. La sobrecarga puede deberse a errores de diseño, mal uso o cambios inesperados en las condiciones operativas.
- Defectos de Fabricación
- Los defectos en el material del engranaje, como inclusiones no metálicas o grietas internas, pueden debilitar el engranaje y hacerlo susceptible a fallos bajo condiciones normales de operación.
- Lubricación Inadecuada
- La falta de lubricación adecuada puede llevar a un aumento del desgaste y el calentamiento de los engranajes, acelerando su deterioro.
Técnicas de Identificación de Defectos en Engranajes
- Análisis de Vibraciones
- Esta técnica se utiliza para detectar irregularidades en el comportamiento vibratorio de los engranajes. Los defectos en los engranajes pueden causar patrones de vibración específicos que pueden ser identificados mediante el análisis de señales de vibración.
- Análisis de Aceite
- El análisis de las partículas presentes en el lubricante puede proporcionar información valiosa sobre el desgaste de los engranajes. Las partículas de metal en el aceite pueden indicar desgaste abrasivo o fatiga de superficie.
- Inspección Visual
- La inspección visual de los engranajes puede revelar signos de desgaste, picaduras, grietas y otros defectos. Se utilizan herramientas como lupas y microscopios para una inspección más detallada.
- Pruebas No Destructivas (NDT)
- Técnicas como la radiografía, la ultrasonografía y la inspección por partículas magnéticas pueden ser utilizadas para detectar defectos internos y superficiales en los engranajes sin causar daños adicionales.
- Termografía Infrarroja
- El monitoreo de la temperatura de los engranajes puede ayudar a identificar problemas de lubricación y sobrecarga. Las áreas calientes en un engranaje pueden indicar fricción excesiva y desgaste.
Mejores Prácticas para la Prevención y Corrección de Defectos
- Mantenimiento Regular
- La implementación de un programa de mantenimiento preventivo puede ayudar a identificar y corregir defectos en sus etapas iniciales, antes de que causen fallos mayores.
- Lubricación Adecuada
- Utilizar el lubricante adecuado y mantener un programa de lubricación regular es crucial para reducir el desgaste y prevenir la fricción excesiva.
- Monitoreo Continuo
- El uso de sistemas de monitoreo continuo para el análisis de vibraciones y la termografía puede proporcionar alertas tempranas sobre posibles problemas.
- Alineación Precisa
- Asegurar una alineación precisa de los ejes y componentes relacionados puede prevenir la distribución desigual de cargas y el desgaste prematuro.
- Capacitación del Personal
- Capacitar al personal en la identificación de defectos y en las mejores prácticas de mantenimiento puede mejorar significativamente la confiabilidad de los engranajes.
La identificación de defectos en engranajes es un proceso crítico que requiere una combinación de técnicas de monitoreo avanzadas y prácticas de mantenimiento adecuadas. Al comprender las causas comunes de los defectos y utilizar las técnicas adecuadas para su identificación, las industrias pueden mejorar la durabilidad y eficiencia de sus sistemas de engranajes, reduciendo los costos de mantenimiento y los tiempos de inactividad no planificados. Implementar un enfoque integral para el mantenimiento y monitoreo de los engranajes es esencial para asegurar su desempeño óptimo y prolongar su vida útil.