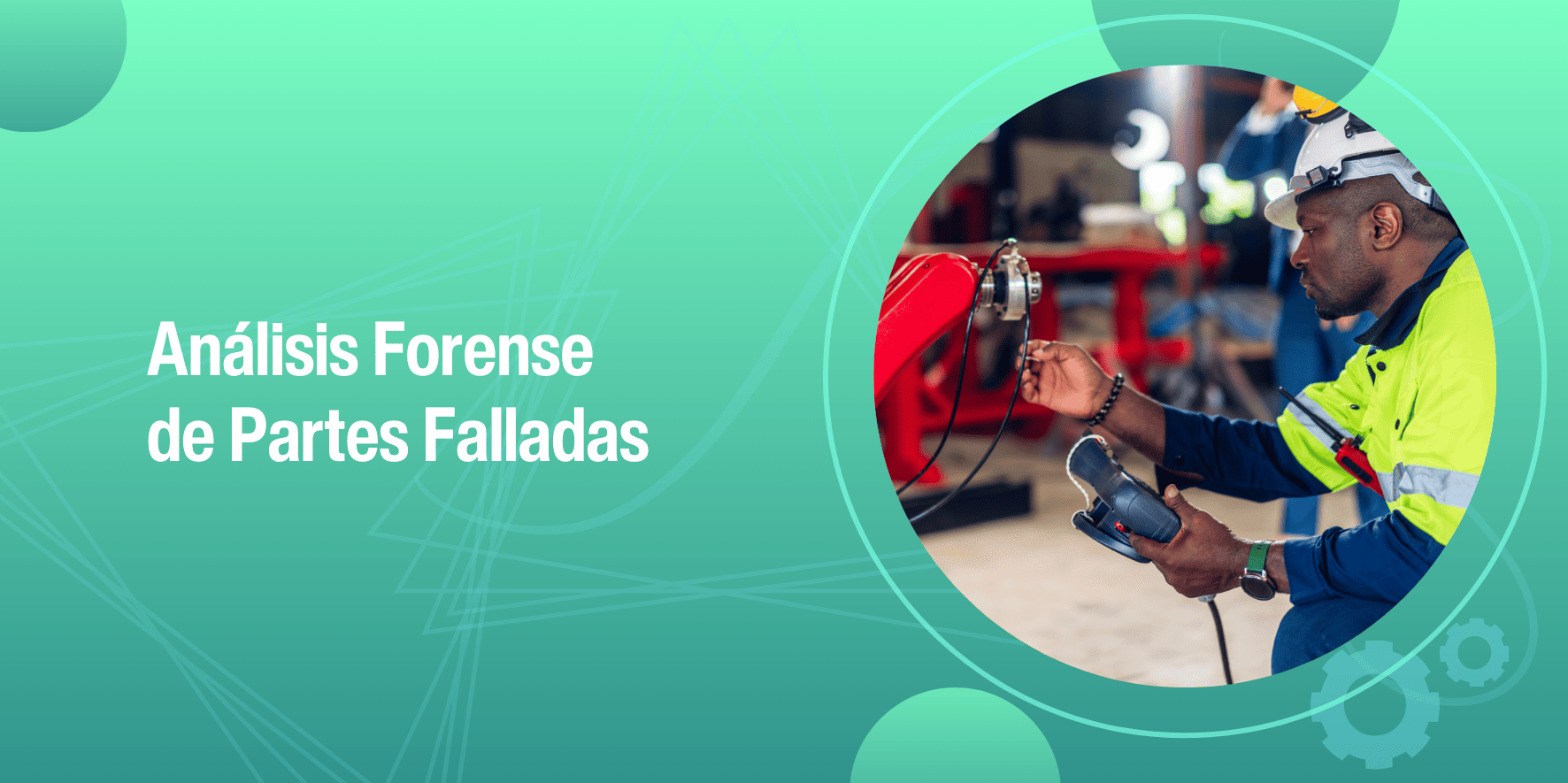
El análisis forense de partes falladas es un proceso crucial en la ingeniería y el mantenimiento industrial. Su objetivo principal es identificar las causas raíz de fallas en componentes o equipos, permitiendo prevenir futuros incidentes y optimizar el diseño, la fabricación y el mantenimiento. Este enfoque combina conocimientos técnicos y científicos para abordar problemas complejos y minimizar costos asociados a fallas inesperadas.
Análisis Forense de Partes Falladas: Una Guía para Entender y Prevenir Fallas en Equipos
El análisis forense de partes falladas es un proceso crucial en la ingeniería y el mantenimiento industrial. Su objetivo principal es identificar las causas raíz de fallas en componentes o equipos, permitiendo prevenir futuros incidentes y optimizar el diseño, la fabricación y el mantenimiento. Este enfoque combina conocimientos técnicos y científicos para abordar problemas complejos y minimizar costos asociados a fallas inesperadas.
¿Qué es el análisis forense de partes falladas?
El análisis forense de partes falladas es una técnica interdisciplinaria que utiliza principios de ingeniería, materiales y ciencias forenses para investigar por qué un componente falló. Este proceso busca responder preguntas como:
- ¿Qué causó la falla?
- ¿Cuándo comenzó el problema?
- ¿Cómo se propagó hasta fallar completamente?
- ¿Cómo prevenir que ocurra de nuevo?
El análisis forense no solo es reactivo, sino también preventivo, ya que ofrece datos críticos para mejorar sistemas y evitar daños más graves.
Importancia del análisis forense de fallas
Este tipo de análisis tiene aplicaciones prácticas significativas en múltiples sectores industriales:
- Aumento de la seguridad: En industrias como la aeronáutica, el transporte o la energía, prevenir fallas catastróficas es crucial para proteger vidas.
- Reducción de costos: Identificar las causas raíz ayuda a evitar reparaciones innecesarias y paradas operativas prolongadas.
- Cumplimiento normativo: Asegura que los equipos cumplan con regulaciones técnicas y de seguridad.
- Mejora del diseño: Proporciona información para optimizar componentes y sistemas en futuras iteraciones.
- Resolución de disputas legales: En caso de litigios por fallas, proporciona evidencia técnica sólida.
Etapas clave en el análisis forense de fallas
El análisis forense sigue un proceso estructurado que garantiza una investigación exhaustiva y objetiva:
1. Recolección de datos iniciales
Antes de tocar la pieza fallada, es fundamental recopilar toda la información posible sobre el contexto de la falla:
- Condiciones de operación en el momento del fallo.
- Historial de mantenimiento del equipo.
- Especificaciones técnicas del componente.
- Informes de incidentes relacionados.
2. Inspección visual
La inspección inicial permite identificar signos evidentes de daño, como:
- Fracturas o grietas visibles.
- Deformaciones plásticas.
- Desgaste excesivo o corrosión.
- Cambios de color o textura (indicativos de sobrecalentamiento).
3. Análisis macroscópico
Se examinan las superficies y características generales de la falla para identificar patrones clave:
- Fracturas frágiles: Asociadas con materiales quebradizos.
- Fracturas dúctiles: Indicativas de deformación antes del fallo.
- Pitting o picaduras: Relacionadas con corrosión o fatiga.
4. Análisis microscópico
Se utilizan técnicas avanzadas para estudiar la microestructura y superficies de falla:
- Microscopía electrónica de barrido (SEM): Permite analizar detalles precisos de fracturas.
- Espectroscopía de energía dispersiva (EDS): Identifica composiciones químicas.
- Microscopía óptica: Analiza características metalúrgicas y texturas superficiales.
5. Pruebas mecánicas y químicas
Se realizan ensayos específicos para evaluar propiedades y condiciones del material:
- Ensayos de dureza: Determinan si el material cumple con las especificaciones.
- Pruebas de tracción y fatiga: Miden resistencia y durabilidad.
- Análisis químico: Detecta posibles contaminantes o variaciones en la composición.
6. Análisis de causas raíz
Con base en los datos recolectados, se identifican los factores que contribuyeron a la falla. Esto puede incluir:
- Sobrecarga mecánica.
- Defectos de fabricación o materiales.
- Condiciones operativas adversas (vibración, temperatura extrema).
- Errores humanos o de diseño.
7. Recomendaciones preventivas
Finalmente, el análisis culmina con un informe que detalla las causas raíz y sugiere medidas para prevenir incidentes futuros. Estas recomendaciones pueden incluir cambios en el diseño, ajustes en el mantenimiento o mejoras en la operación.
Tipos comunes de fallas analizadas
1. Fallas por fatiga
Ocurren debido a ciclos repetidos de carga y descarga, que provocan grietas microscópicas que eventualmente se propagan.
2. Fallas por corrosión
La exposición a entornos corrosivos degrada los materiales, reduciendo su resistencia y causando daños estructurales.
3. Fallas por sobrecarga
Exceder los límites de diseño provoca deformación plástica o fractura instantánea.
4. Fallas térmicas
Cambios extremos de temperatura pueden inducir tensiones internas que comprometen el material.
5. Fallas por defecto de fabricación
Incluyen inclusiones, soldaduras deficientes o tratamientos térmicos mal ejecutados.
Herramientas y técnicas utilizadas
El análisis forense de fallas emplea una amplia gama de herramientas y métodos avanzados, tales como:
- Tomografía computarizada (CT): Genera imágenes internas de piezas sin dañarlas.
- Difracción de rayos X (XRD): Identifica fases cristalinas en materiales.
- Ensayos no destructivos (END): Como ultrasonido o líquidos penetrantes, para identificar defectos ocultos.
Desafíos del análisis forense
Aunque es una técnica poderosa, el análisis de fallas presenta algunos retos:
- Evidencia limitada: En ocasiones, las piezas están severamente dañadas o contaminadas, dificultando la evaluación.
- Intervenciones previas: Reparaciones realizadas antes del análisis pueden alterar la evidencia.
- Ambigüedad en las causas: Las fallas suelen ser el resultado de múltiples factores combinados.
Aplicaciones en la industria
El análisis forense de fallas es relevante en numerosas industrias, incluyendo:
- Aeroespacial: Fallas en motores, fuselajes y sistemas críticos.
- Energía: Turbinas, generadores y equipos de transmisión.
- Automotriz: Componentes del tren motriz y sistemas de suspensión.
- Manufactura: Herramientas, moldes y maquinaria.
El análisis forense de partes falladas no solo es un instrumento para resolver problemas, sino una herramienta estratégica para la mejora continua en el diseño, fabricación y mantenimiento de equipos. Al comprender las causas raíz de las fallas, las industrias pueden minimizar riesgos, optimizar recursos y fortalecer la confiabilidad de sus operaciones.
Invertir en este tipo de análisis es clave para avanzar hacia un entorno industrial más seguro, eficiente y competitivo. El conocimiento es la mejor defensa contra la repetición de errores.