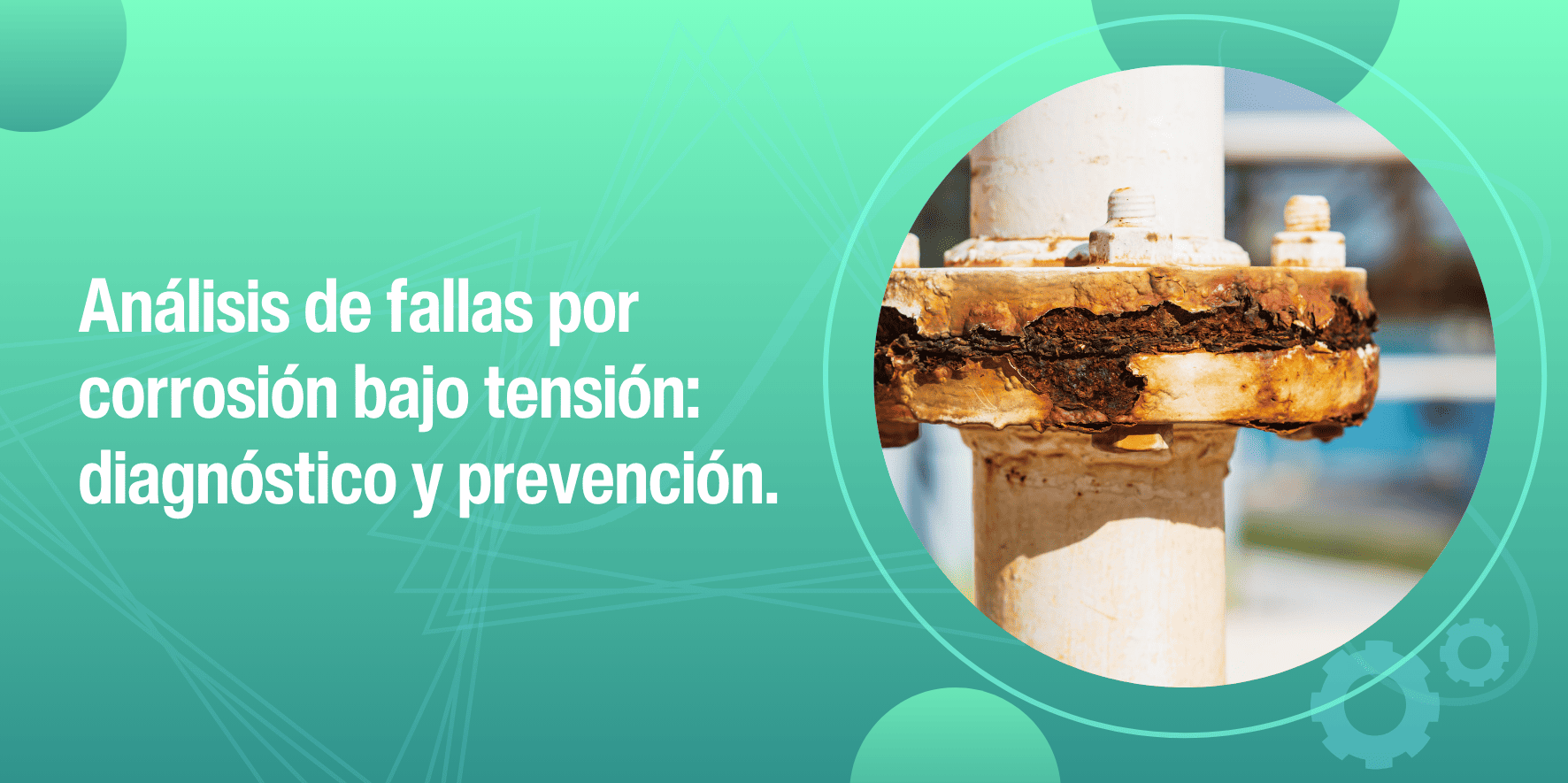
La corrosión bajo tensión (Stress Corrosion Cracking, SCC) es una de las principales causas de fallas en materiales metálicos, especialmente en entornos agresivos. Este fenómeno, que combina esfuerzos mecánicos y corrosión química, puede provocar fracturas inesperadas en componentes críticos, con consecuencias significativas en términos de seguridad y costos.
En este artículo, exploraremos los principios fundamentales del SCC, las técnicas para diagnosticarlo y las estrategias efectivas para prevenir este tipo de fallas.
Análisis de fallas por corrosión bajo tensión: diagnóstico y prevención
La corrosión bajo tensión (Stress Corrosion Cracking, SCC) es una de las principales causas de fallas en materiales metálicos, especialmente en entornos agresivos. Este fenómeno, que combina esfuerzos mecánicos y corrosión química, puede provocar fracturas inesperadas en componentes críticos, con consecuencias significativas en términos de seguridad y costos.
En este artículo, exploraremos los principios fundamentales del SCC, las técnicas para diagnosticarlo y las estrategias efectivas para prevenir este tipo de fallas.
¿Qué es la corrosión bajo tensión?
La corrosión bajo tensión es un mecanismo de falla que ocurre cuando un material está sometido simultáneamente a:
- Esfuerzos mecánicos: Pueden ser externos (como cargas aplicadas) o internos (como tensiones residuales).
- Un entorno corrosivo: Un medio químico que degrada el material, como soluciones salinas, ácidos o álcalis.
Este fenómeno es insidioso porque puede desarrollarse sin señales visibles hasta que ocurre una fractura catastrófica.
Factores que influyen en el SCC
Material
- Aleaciones susceptibles: Acero inoxidable, aleaciones de aluminio, cobre y níquel son particularmente vulnerables.
- Microestructura: Fases secundarias o impurezas en los límites de grano pueden acelerar el SCC.
Entorno
- Presencia de iones específicos: Cloruros y álcalis son agentes comunes que promueven el SCC.
- Condiciones ambientales: Alta temperatura y humedad intensifican la corrosión bajo tensión.
Esfuerzos aplicados
- Tensiones residuales: Generadas durante procesos de fabricación como soldadura o deformación.
- Cargas externas: Aquellas asociadas al uso del componente en su entorno operativo.
Diagnóstico del SCC
Un análisis de fallas eficaz implica identificar los signos característicos de SCC y confirmar su presencia mediante pruebas avanzadas.
Inspección visual
- Grietas finas y ramificadas, a menudo invisibles a simple vista.
- Ubicación en áreas sometidas a esfuerzos elevados o expuestas a agentes corrosivos.
Análisis macroscópico y microscópico
- Superficie de fractura: La grieta sigue típicamente los límites de grano (fractura intergranular), aunque también puede ser transgranular en algunos casos.
- Técnicas avanzadas:
- Microscopía electrónica de barrido (SEM): Permite observar la topografía de la fractura y analizar características como corrosión localizada o productos de corrosión.
- Microscopía de transmisión (TEM): Revela detalles a nivel atómico, como segregación de elementos en los límites de grano.
Análisis químico
- Identificación de agentes corrosivos en el entorno operativo mediante espectroscopia de emisión atómica o análisis de difracción de rayos X (XRD).
Pruebas de esfuerzo y corrosión
- Pruebas aceleradas: Exponer el material a un entorno controlado que simule condiciones reales para observar la susceptibilidad al SCC.
- Pruebas de flexión bajo carga constante: Usadas para evaluar el tiempo hasta la fractura en presencia de agentes corrosivos.
Prevención del SCC
Prevenir la corrosión bajo tensión requiere una combinación de estrategias relacionadas con el diseño, el material y el entorno operativo.
Selección de materiales
- Uso de materiales resistentes al SCC:
- Acero inoxidable con bajo contenido de carbono (por ejemplo, grados 316L o 2205).
- Aleaciones especiales resistentes a la corrosión, como Hastelloy o Inconel.
- Tratamientos térmicos:
- Procesos como el recocido o el alivio de tensiones para eliminar tensiones residuales internas.
Control del entorno
- Eliminación de agentes corrosivos:
- Uso de recubrimientos protectores para aislar el material del medio agresivo.
- Deshumidificación en áreas con alta humedad.
- Modificación del medio:
- Inhibidores de corrosión para reducir la agresividad química del entorno.
Reducción de tensiones
- Diseño optimizado:
- Minimizar concentradores de tensión como bordes afilados o cambios abruptos en la geometría.
- Uso de uniones atornilladas en lugar de soldaduras en áreas críticas.
- Post-tratamientos mecánicos:
- Shot peening: Introduce tensiones compresivas en la superficie para contrarrestar las tensiones de tracción.
Mantenimiento proactivo
- Monitoreo regular: Inspección visual y no destructiva para detectar grietas incipientes.
- Reemplazo preventivo: Sustitución de componentes críticos antes de que se acerquen al final de su vida útil esperada.
Ejemplos de SCC en la industria
Aeronáutica
- Grietas en fuselajes de aviones debido a la exposición a humedad y tensiones cíclicas.
Petróleo y gas
- Tuberías y equipos sometidos a esfuerzos elevados y expuestos a agua salada y gases ácidos como el H₂S.
Plantas químicas
- Tanques de almacenamiento hechos de acero inoxidable que fallan debido a agentes agresivos en procesos industriales.
El análisis de fallas por corrosión bajo tensión es un paso esencial para identificar las causas fundamentales de este fenómeno y desarrollar estrategias efectivas de prevención. La combinación de técnicas de inspección, análisis químico y ensayos mecánicos proporciona una visión integral que ayuda a mitigar riesgos en sistemas críticos.
La prevención efectiva requiere una selección adecuada de materiales, control del entorno y un diseño robusto, combinado con programas de mantenimiento que permitan detectar problemas antes de que se conviertan en fallas catastróficas. Entender y combatir el SCC no solo mejora la seguridad, sino que también optimiza los costos y la confiabilidad en aplicaciones industriales.