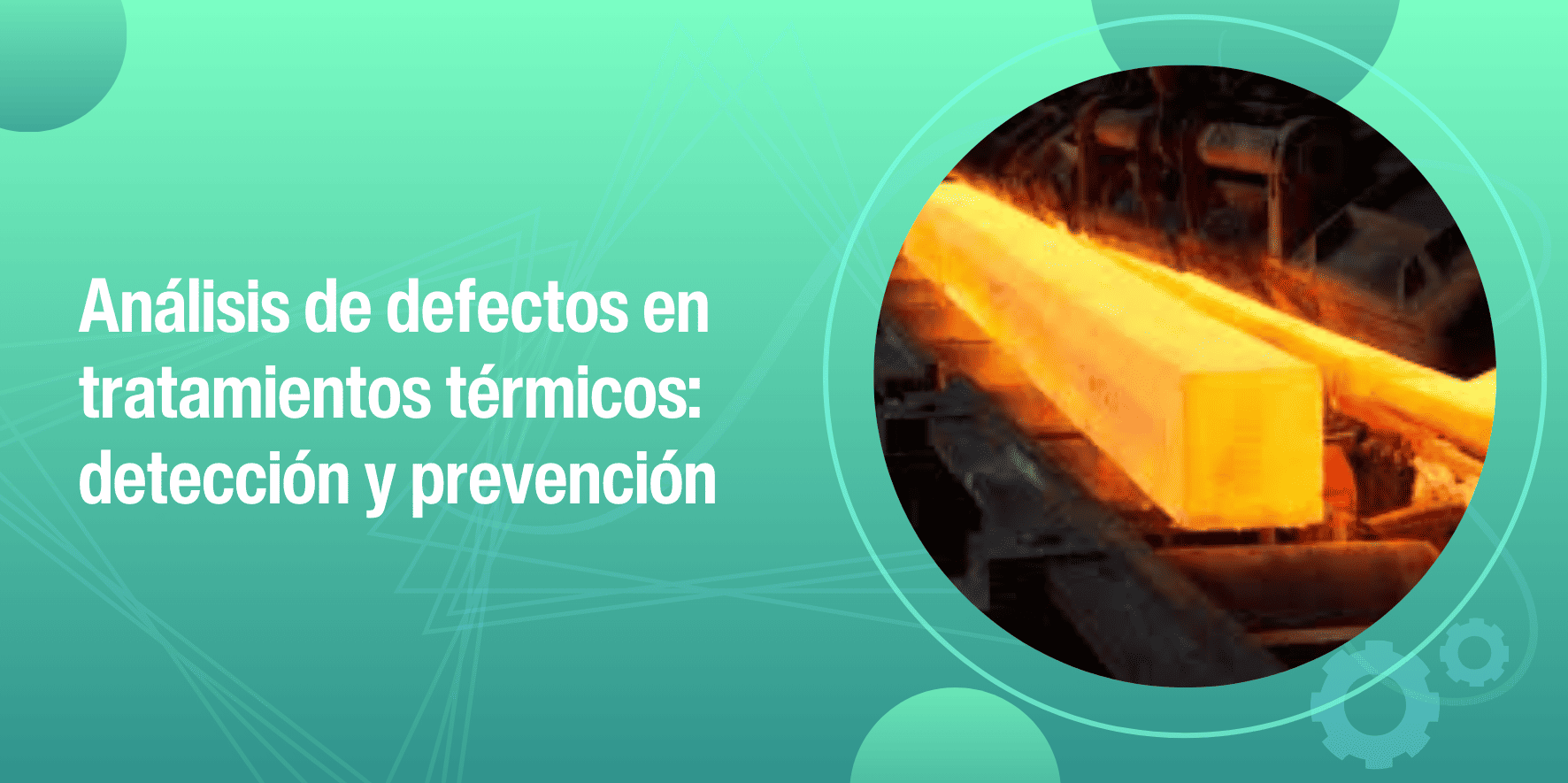
Los tratamientos térmicos son procesos clave en la fabricación y mantenimiento de componentes metálicos, ya que permiten modificar sus propiedades mecánicas, microestructura y resistencia al desgaste. Sin embargo, si no se controlan adecuadamente los parámetros del proceso, pueden aparecer defectos que comprometen la integridad y funcionalidad del material.
Estos defectos pueden manifestarse como fisuras, distorsiones, variaciones de dureza, descarbonización y fragilización, entre otros. La detección temprana y la implementación de estrategias de prevención son fundamentales para evitar costos elevados por retrabajo, fallas prematuras o rechazo de piezas.
En este artículo, exploraremos los defectos más comunes en los tratamientos térmicos, sus causas, métodos de detección y estrategias para prevenirlos.
Análisis de Defectos en Tratamientos Térmicos: Detección y Prevención
Los tratamientos térmicos son procesos clave en la fabricación y mantenimiento de componentes metálicos, ya que permiten modificar sus propiedades mecánicas, microestructura y resistencia al desgaste. Sin embargo, si no se controlan adecuadamente los parámetros del proceso, pueden aparecer defectos que comprometen la integridad y funcionalidad del material.
Estos defectos pueden manifestarse como fisuras, distorsiones, variaciones de dureza, descarbonización y fragilización, entre otros. La detección temprana y la implementación de estrategias de prevención son fundamentales para evitar costos elevados por retrabajo, fallas prematuras o rechazo de piezas.
En este artículo, exploraremos los defectos más comunes en los tratamientos térmicos, sus causas, métodos de detección y estrategias para prevenirlos.
- Principales Defectos en Tratamientos Térmicos
Dependiendo del tipo de tratamiento térmico aplicado (templado, revenido, normalizado, recocido, carburización, nitruración, etc.), pueden presentarse diferentes defectos. Los más comunes incluyen:
1.1 Distorsión y Deformaciones
🔹 Descripción: Se producen cambios dimensionales y de forma en la pieza debido a variaciones en la velocidad de enfriamiento y distribución de tensiones internas.
🔹 Causas:
- Enfriamiento desigual durante el templado.
- Diseño inadecuado de la pieza (espesores desiguales).
- Variaciones en la composición del material.
- Aplicación de un tratamiento térmico incorrecto para la geometría de la pieza.
🔹 Impacto:
⚠ Desajustes en tolerancias dimensionales.
⚠ Dificultades en el ensamblaje de componentes.
⚠ Necesidad de mecanizado adicional o descarte de piezas.
🔹 Estrategias de prevención:
✅ Controlar la velocidad de calentamiento y enfriamiento.
✅ Utilizar soportes o fijaciones durante el proceso.
✅ Aplicar tratamientos térmicos intermedios para aliviar tensiones.
✅ Considerar la composición del material y su respuesta al tratamiento.
1.2 Grietas y Fisuración
🔹 Descripción: Las grietas pueden aparecer durante o después del tratamiento térmico debido a tensiones internas excesivas.
🔹 Causas:
- Enfriamiento brusco en el templado.
- Alto contenido de carbono en el material.
- Presencia de inclusiones o defectos previos en la microestructura.
- Falta de un revenido adecuado después del templado.
🔹 Impacto:
⚠ Reducción drástica de la resistencia mecánica.
⚠ Mayor susceptibilidad a la fractura por fatiga.
⚠ Posible fallo catastrófico del componente en operación.
🔹 Estrategias de prevención:
✅ Seleccionar un medio de enfriamiento adecuado (aceite, agua, aire).
✅ Aplicar revenidos inmediatamente después del templado para reducir tensiones.
✅ Inspeccionar la microestructura antes del tratamiento térmico.
✅ Evitar cambios bruscos de temperatura en materiales de alta dureza.
1.3 Variaciones en la Dureza y Propiedades Mecánicas
🔹 Descripción: Se presentan cuando la dureza no es uniforme en la pieza o no se alcanza la dureza esperada tras el tratamiento térmico.
🔹 Causas:
- Diferencias en la velocidad de enfriamiento dentro de la pieza.
- Falta de austenización completa antes del templado.
- Contaminación superficial que impide la difusión térmica uniforme.
- Tratamiento térmico incorrecto para la aleación utilizada.
🔹 Impacto:
⚠ Pérdida de resistencia al desgaste.
⚠ Reducción de la capacidad de carga del material.
⚠ Desempeño inconsistente en condiciones de servicio.
🔹 Estrategias de prevención:
✅ Asegurar una temperatura de austenización homogénea antes del enfriamiento.
✅ Utilizar medios de enfriamiento controlados y homogéneos.
✅ Verificar la composición química del material y su respuesta al tratamiento.
✅ Implementar controles de calidad en cada etapa del proceso.
1.4 Descarbonización y Oxidación
🔹 Descripción: Se produce una pérdida de carbono en la superficie del material, reduciendo su dureza y resistencia al desgaste.
🔹 Causas:
- Exposición prolongada al aire u oxígeno a altas temperaturas.
- Falta de protección adecuada en el horno (atmósfera controlada).
- Uso inadecuado de recubrimientos o sales protectoras.
🔹 Impacto:
⚠ Reducción de la dureza superficial.
⚠ Mayor susceptibilidad al desgaste y fatiga.
⚠ Necesidad de rectificado o reposición del material afectado.
🔹 Estrategias de prevención:
✅ Utilizar atmósferas protectoras en hornos de tratamiento térmico (nitrógeno, argón).
✅ Aplicar recubrimientos protectores antes del tratamiento.
✅ Controlar la exposición de la pieza a temperaturas elevadas.
2. Métodos de Detección de Defectos en Tratamientos Térmicos
Para garantizar la calidad de los componentes tratados térmicamente, se deben aplicar diversas técnicas de inspección y ensayo:
📌 Ensayos de dureza (Rockwell, Vickers, Brinell): Permiten verificar que la dureza alcanzada en la pieza sea la esperada.
📌 Metalografía: Mediante microscopía óptica o electrónica se analizan los cambios en la microestructura.
📌 Ultrasonido: Detecta grietas internas y discontinuidades en la pieza.
📌 Líquidos penetrantes y partículas magnéticas: Identifican grietas superficiales y defectos en materiales ferromagnéticos.
📌 Medición de distorsión y deformaciones: Se comparan dimensiones antes y después del tratamiento para evaluar cambios no deseados.
- Caso Práctico: Falla en un Eje de Transmisión por Defectos en Tratamiento Térmico
Un caso emblemático de defectos en tratamientos térmicos ocurrió en la industria automotriz, cuando se detectaron fallas prematuras en ejes de transmisión de acero sometidos a templado y revenido.
📌 Problema: Los ejes mostraban fracturas en condiciones normales de operación.
📌 Análisis: Se realizaron ensayos metalográficos y de dureza, detectándose una microestructura frágil con presencia de grietas internas.
📌 Causa: Se identificó que el revenido no se realizó correctamente, lo que generó tensiones residuales y fragilización del material.
📌 Solución: Se ajustaron los parámetros de revenido y se implementó un control más estricto de la temperatura.
Tras estos cambios, la vida útil de los ejes se incrementó significativamente, reduciendo costos por fallas y mantenimiento.
Los defectos en tratamientos térmicos pueden comprometer seriamente el desempeño de los componentes metálicos. La distorsión, las grietas, la descarbonización y las variaciones de dureza son problemas recurrentes que pueden ser prevenidos con controles adecuados de temperatura, velocidad de enfriamiento y métodos de inspección rigurosos.
La detección temprana de defectos y la aplicación de estrategias correctivas garantizan la calidad de los componentes y prolongan su vida útil en condiciones de servicio exigentes.