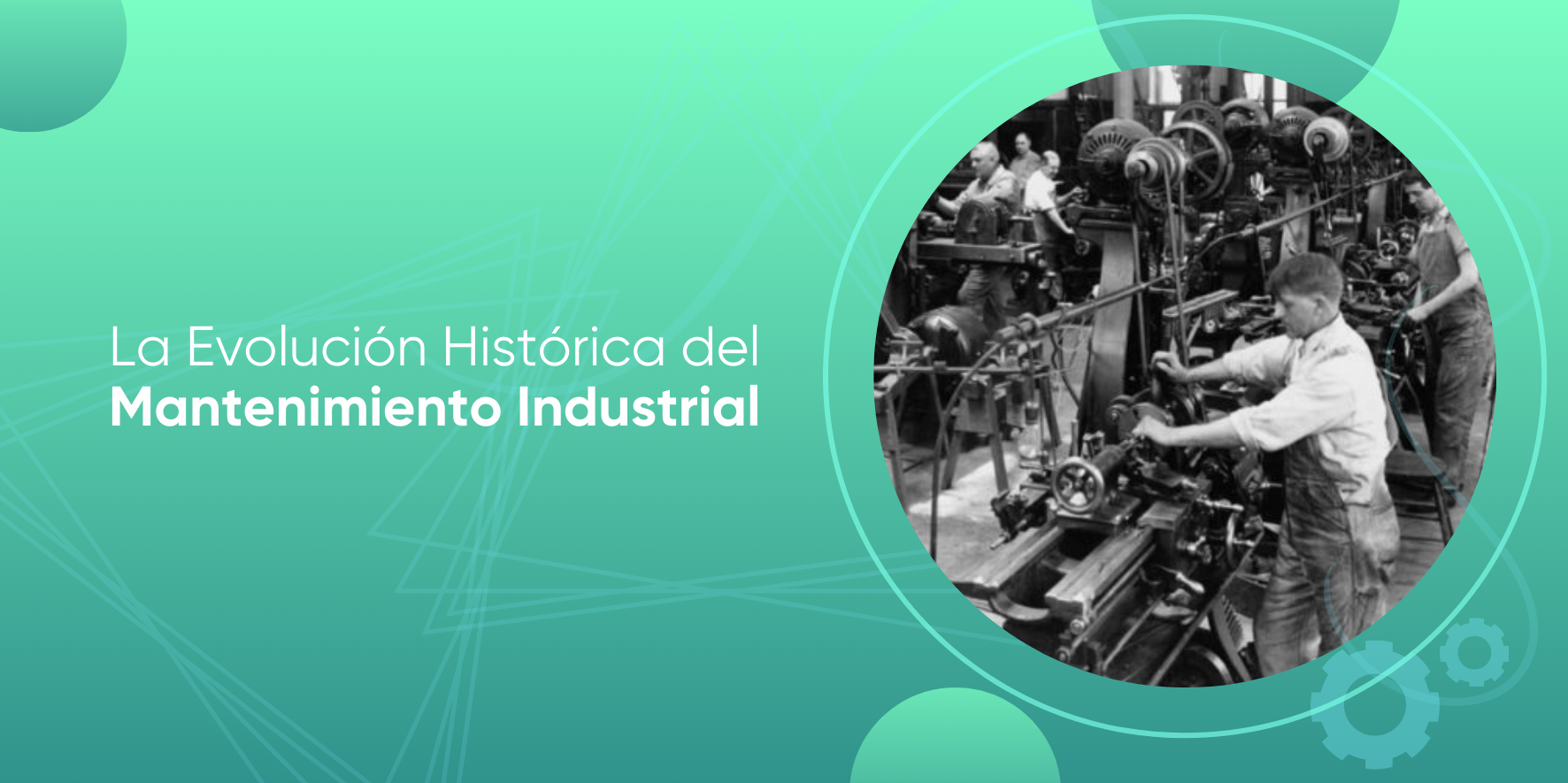
La Evolución Histórica del Mantenimiento Industrial: Desde los Orígenes hasta la Era Digital
El mantenimiento industrial, a lo largo de la historia, ha experimentado una evolución significativa, desde sus modestos comienzos hasta convertirse en una disciplina crucial en la gestión de activos y la producción eficiente. En este artículo, exploraremos la fascinante historia del mantenimiento industrial, destacando los hitos clave que han dado forma a su desarrollo a lo largo de los siglos.
- Orígenes y Antecedentes
El mantenimiento industrial tiene sus raíces en las antiguas civilizaciones, donde las comunidades dependían de la reparación y el mantenimiento de herramientas y equipos para la supervivencia. Desde los primeros artesanos que afilaban sus herramientas de piedra hasta las sociedades agrícolas que mantenían sus arados y cosechadoras, el mantenimiento ha sido una parte integral de la vida humana desde tiempos inmemoriales.
- Revolución Industrial y Surgimiento del Mantenimiento Moderno
La Revolución Industrial marcó un punto de inflexión en la historia del mantenimiento industrial. Con la introducción de la maquinaria impulsada por vapor y posteriormente por electricidad, surgió la necesidad de mantener estos nuevos equipos en funcionamiento óptimo. Esto llevó al desarrollo de las primeras prácticas de mantenimiento planificado y predictivo, destinadas a minimizar los tiempos de inactividad y maximizar la productividad en las fábricas y plantas industriales.
- Surgimiento de la Gestión del Mantenimiento como Disciplina
A medida que las operaciones industriales crecían en tamaño y complejidad, también lo hacía la necesidad de una gestión más formalizada del mantenimiento. En la década de 1950, surgieron los primeros enfoques sistemáticos para la gestión del mantenimiento, como el mantenimiento preventivo y el mantenimiento centrado en la confiabilidad (RCM). Estos enfoques se basaban en la idea de que el mantenimiento debería ser planificado y proactivo, en lugar de reactivo.
- Avances Tecnológicos y la Era Digital
En las últimas décadas, los avances tecnológicos han transformado radicalmente el campo del mantenimiento industrial. La introducción de sistemas de gestión de mantenimiento asistido por computadora (CMMS), la implementación de tecnologías de monitoreo remoto y la adopción de análisis de datos avanzados han permitido una gestión más eficiente y predictiva de los activos industriales. La Industria 4.0 ha llevado esta evolución un paso más allá, con la integración de tecnologías como el Internet de las Cosas (IoT), la inteligencia artificial (IA) y la realidad aumentada (RA) en las operaciones de mantenimiento.
- El Futuro del Mantenimiento Industrial
A medida que nos adentramos en el futuro, el mantenimiento industrial continuará evolucionando para adaptarse a los nuevos desafíos y oportunidades que surjan. Se espera que la digitalización y la automatización jueguen un papel cada vez más importante en la gestión de activos, con un enfoque creciente en la optimización de la eficiencia y la reducción de los costos operativos.
La historia del mantenimiento industrial es una historia de innovación y progreso, desde sus humildes comienzos hasta convertirse en una disciplina compleja y vital en la industria moderna. Al comprender esta evolución histórica, podemos apreciar mejor los desafíos y oportunidades que enfrentamos en el mantenimiento industrial en la actualidad y en el futuro.